A composición química da area cerámica é principalmente Al2O3 e SiO2, e a fase mineral da area cerámica é principalmente a fase de corindón e a fase de mullita, así como unha pequena cantidade de fase amorfa.A refractariedade da area cerámica é xeralmente superior a 1800 °C e é un material refractario de aluminio e silicio de alta dureza.
Características da area cerámica
● Alta refractariedade;
● Pequeno coeficiente de expansión térmica;
● Alta condutividade térmica;
● Forma esférica aproximada, factor de ángulo pequeno, boa fluidez e capacidade de compactación;
● Superficie lisa, sen fendas, sen golpes;
● Material neutro, axeitado para varios materiais metálicos de fundición;
● As partículas teñen unha alta resistencia e non se rompen facilmente;
● O rango de tamaño de partícula é amplo e a mestura pódese personalizar segundo os requisitos do proceso.
Aplicación de area cerámica en fundición de motores
1. Use area de cerámica para resolver as vetas, a pegada da area, o núcleo roto e a deformación do núcleo de area da culata de ferro fundido.
● O bloque de cilindros e a culata son as pezas de fundición máis importantes do motor
● A forma da cavidade interna é complexa e os requisitos de precisión dimensional e limpeza da cavidade interna son altos
● Lote grande

Co fin de garantir a eficiencia da produción e a calidade do produto,
● Xeralmente utilízase a produción da cadea de montaxe de area verde (principalmente liña de estilo hidrostático).
● Os núcleos de area normalmente usan un proceso de caixa fría e area recuberta de resina (núcleo de casca), e algúns núcleos de area usan o proceso de caixa quente.
● Debido á complexa forma do núcleo de area do bloque de cilindros e da fundición da cabeza, algúns núcleos de area teñen unha pequena área de sección transversal, a parte máis delgada dalgúns bloques de cilindros e os núcleos da camisa de auga da culata ten só 3-3,5 mm e a saída de area é estreita, o núcleo de area despois da fundición está rodeado de ferro fundido a alta temperatura durante moito tempo, é difícil limpar a area, é necesario un equipo de limpeza especial, etc. No pasado, toda a area de sílice utilizábase na fundición. produción, o que provocou problemas de pegado de veas e area nas pezas de fundición da camisa de auga do bloque de cilindros e da culata.A deformación do núcleo e os problemas do núcleo roto son moi comúns e difíciles de resolver.
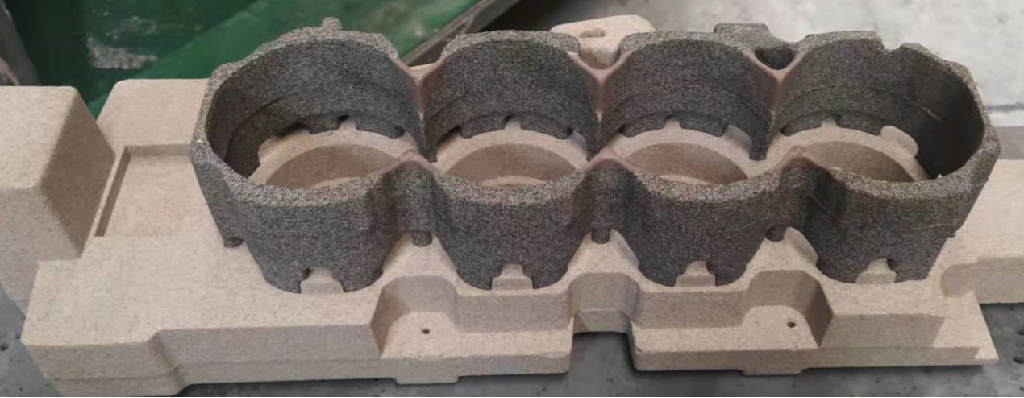
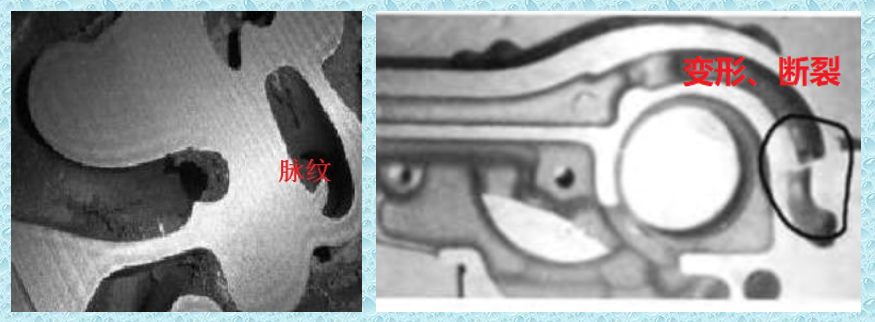
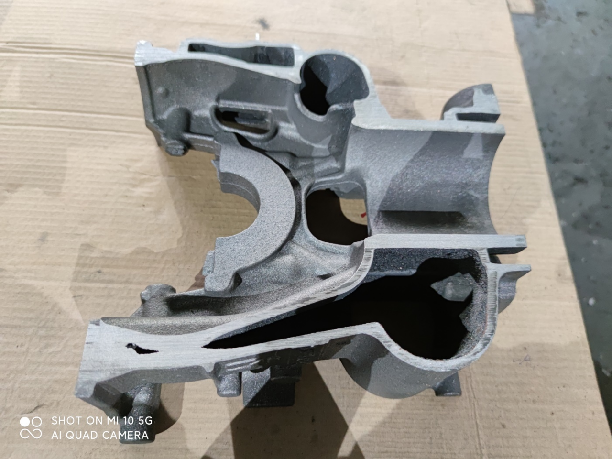
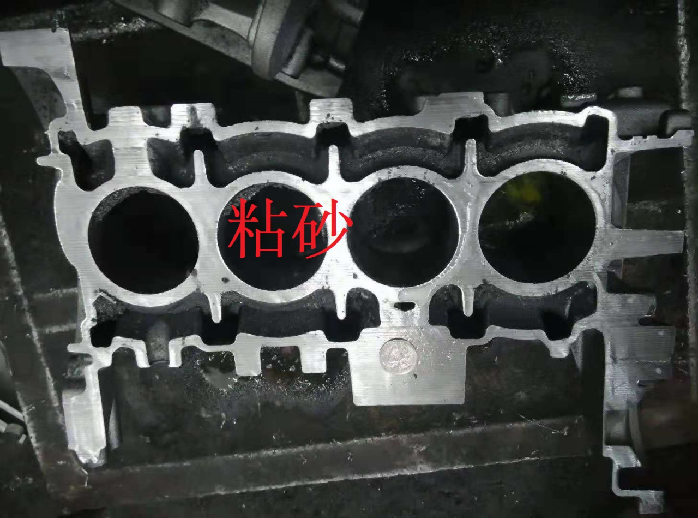
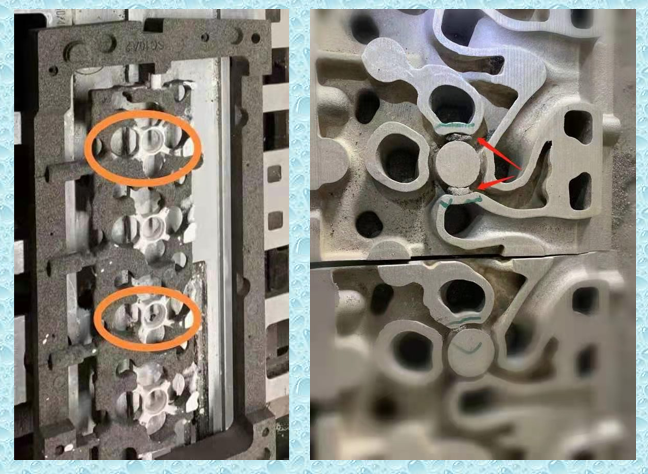
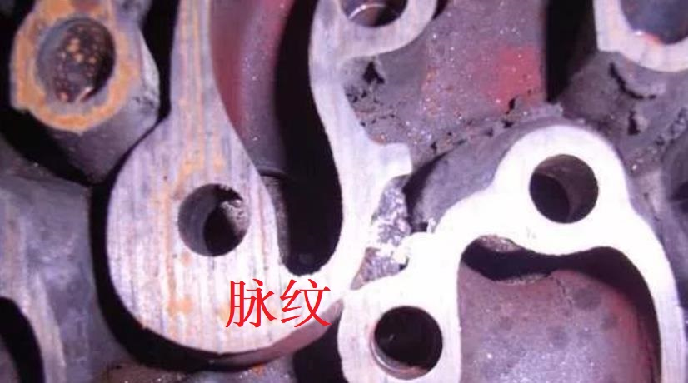
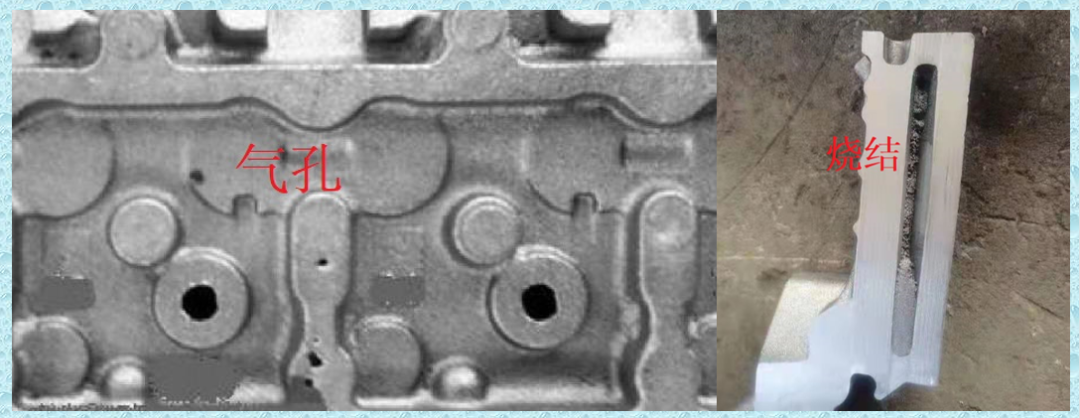
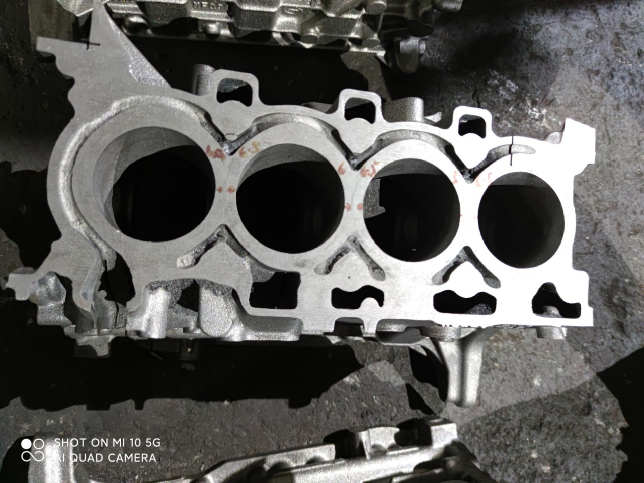
Para resolver estes problemas, a partir de 2010, algunhas empresas nacionais de fundición de motores coñecidas, como FAW, Weichai, Shangchai, Shanxi Xinke, etc., comezaron a investigar e probar a aplicación de area cerámica para producir bloques de cilindros. camisas de auga de culata e pasaxes de aceite.Os núcleos de area iguais eliminan ou reducen eficazmente os defectos como a sinterización da cavidade interna, a adherencia de area, a deformación do núcleo de area e os núcleos rotos.
As seguintes imaxes están feitas con area cerámica cun proceso de caixa fría.
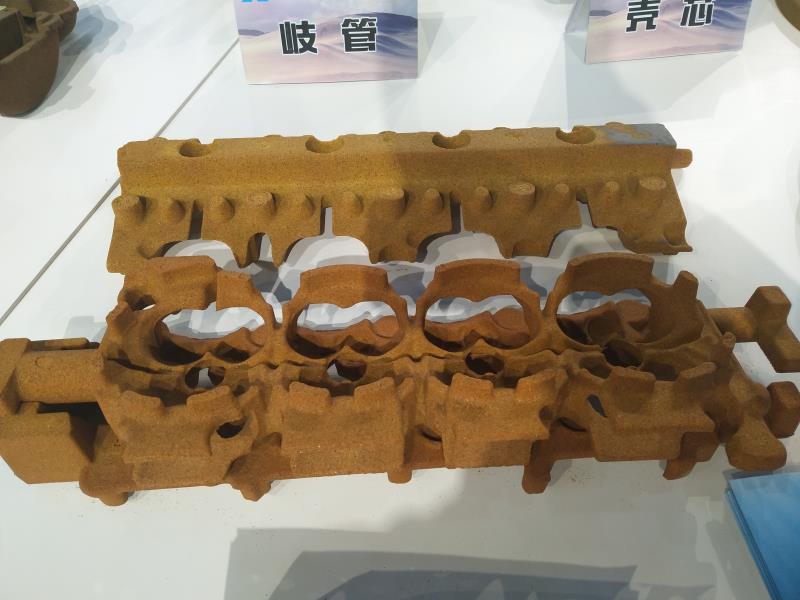
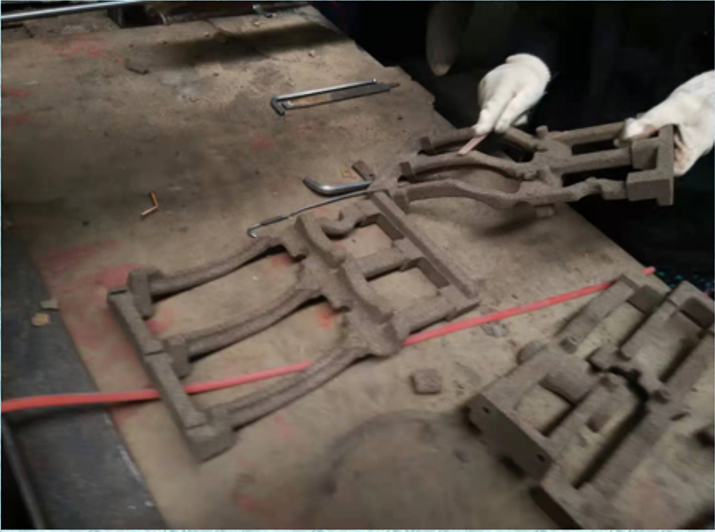
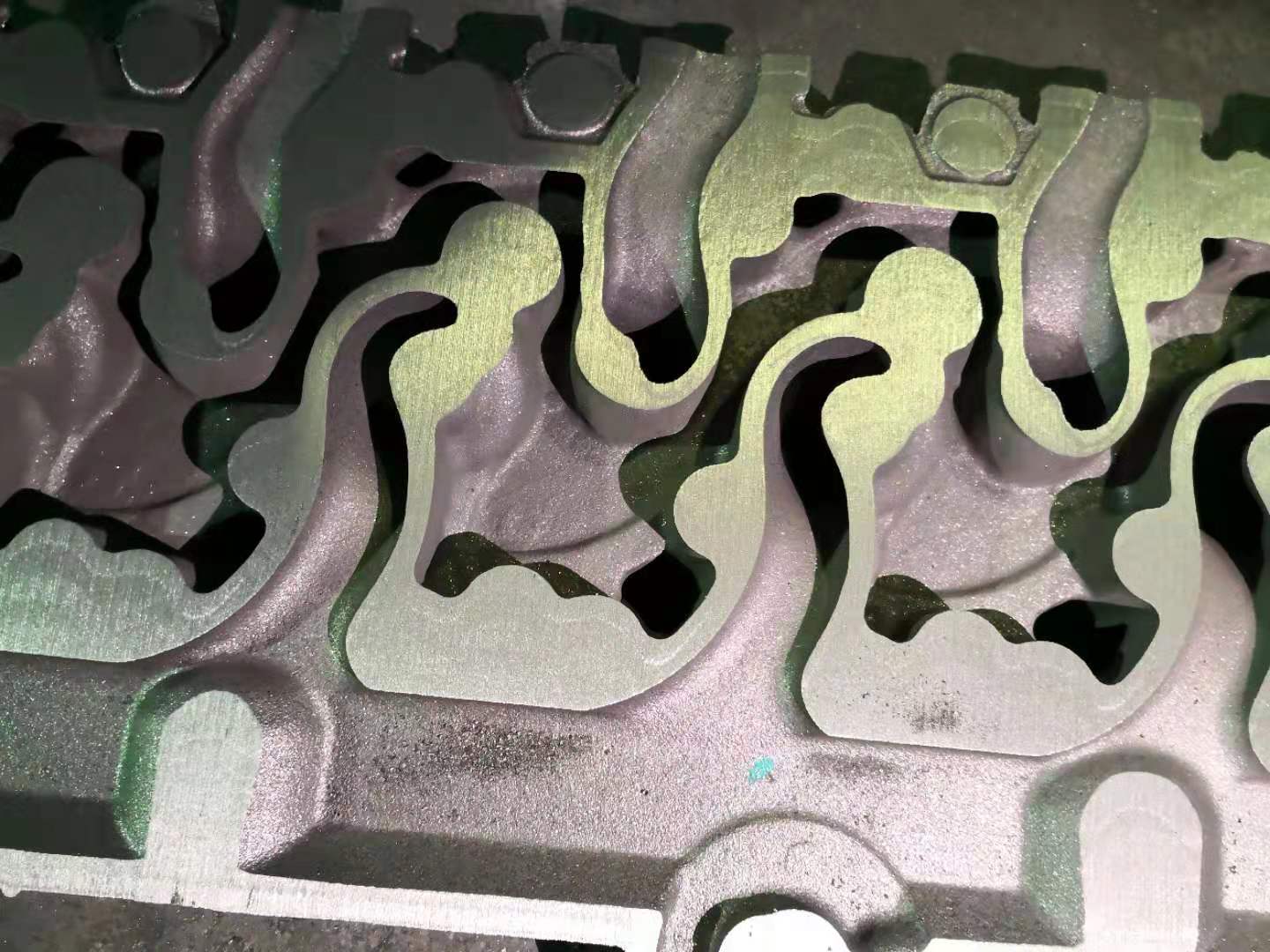
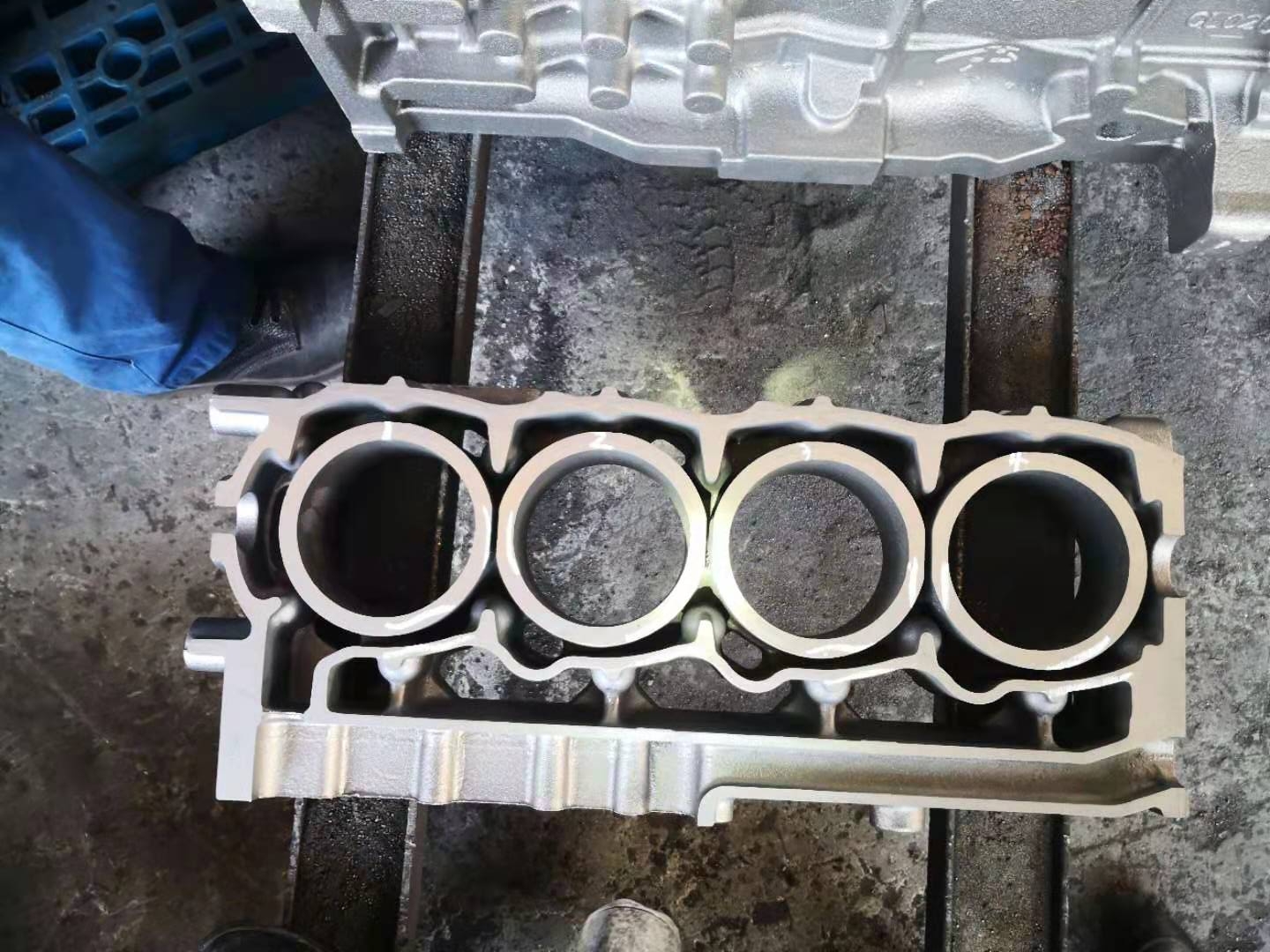
Desde entón, a area de fregado mixta de area cerámica foi promovida gradualmente nos procesos de caixa fría e caixa quente, e aplicouse aos núcleos da camisa de auga da culata.Leva máis de 6 anos en produción estable.O uso actual do núcleo de area de caixa fría é: segundo a forma e o tamaño do núcleo de area, a cantidade de area cerámica engadida é do 30% ao 50%, a cantidade total de resina engadida é do 1,2% ao 1,8% e o a resistencia á tracción é de 2,2-2,7 MPa.(Datos de proba de mostras de laboratorio)
Resumo
As pezas de ferro fundido do bloque de cilindros e da cabeza conteñen moitas estruturas estreitas de cavidades internas e a temperatura de vertido adoita estar entre 1440 e 1500 °C.A parte de paredes finas do núcleo de area sinteriza facilmente baixo a acción do ferro fundido a alta temperatura, como o ferro fundido que se infiltra no núcleo de area, ou produce unha reacción de interface para formar area pegajosa.A refractariedade da area cerámica é superior a 1800 ° C, mentres tanto, a verdadeira densidade da area cerámica é relativamente alta, a enerxía cinética das partículas de area co mesmo diámetro e velocidade é 1,28 veces a das partículas de area de sílice ao disparar area, o que pode aumentar a densidade dos núcleos de area.
Estas vantaxes son as razóns polas que o uso de area cerámica pode resolver o problema de pegar a area na cavidade interna das pezas de fundición da culata.
A camisa de auga, as partes de admisión e escape do bloque de cilindros e da culata adoitan ter defectos de veas.Un gran número de investigacións e prácticas de fundición demostraron que a causa raíz dos defectos de vetas na superficie de fundición é a expansión do cambio de fase da area de sílice, que provoca que o estrés térmico provoque gretas na superficie do núcleo de area, o que provoca ferro fundido. para penetrar nas fendas, a tendencia das veas é maior especialmente no proceso de caixa fría.De feito, a taxa de expansión térmica da area de sílice é do 1,5%, mentres que a taxa de expansión térmica da area cerámica é só do 0,13% (quentada a 1000 °C durante 10 minutos).A posibilidade de rachar é moi pequena onde na superficie do núcleo de area debido á tensión de expansión térmica.O uso de area cerámica no núcleo de area do bloque de cilindros e da culata é actualmente unha solución sinxela e eficaz para o problema das vetas.
Os núcleos de area complicados, de paredes delgadas, longas e estreitas da culata de cilindros e os núcleos de area de canles de aceite do cilindro requiren alta resistencia (incluída a resistencia a altas temperaturas) e tenacidade e, ao mesmo tempo, precisan controlar a xeración de gas da area do núcleo.Tradicionalmente, úsase principalmente o proceso de area revestida.O uso de area cerámica reduce a cantidade de resina e consegue o efecto de alta resistencia e baixa xeración de gas.Debido á mellora continua do rendemento da resina e da area bruta, o proceso de caixa fría substituíu cada vez máis parte do proceso de area recuberta nos últimos anos, mellorando moito a eficiencia da produción e mellorando o ambiente de produción.
2. Aplicación de area cerámica para resolver o problema da deformación do núcleo de area do tubo de escape
Os colectores de escape funcionan en condicións alternas de alta temperatura durante moito tempo e a resistencia á oxidación dos materiais a altas temperaturas afecta directamente a vida útil dos colectores de escape.Nos últimos anos, o país mellorou continuamente os estándares de emisión do escape dos automóbiles, e a aplicación da tecnoloxía catalítica e da tecnoloxía de turbocompresor aumentou significativamente a temperatura de traballo do colector de escape, chegando por riba dos 750 °C.Coa mellora do rendemento do motor, tamén aumentará a temperatura de traballo do colector de escape.Na actualidade, úsase xeralmente aceiro fundido resistente á calor, como ZG 40Cr22Ni10Si2 (JB/T 13044), etc., cunha temperatura resistente á calor de 950 °C-1100 °C.
A cavidade interna do colector de escape xeralmente debe estar libre de fendas, peches fríos, cavidades de contracción, inclusións de escouras, etc. que afectan o rendemento, e a rugosidade da cavidade interna non debe ser superior a Ra25.Ao mesmo tempo, hai regulacións estritas e claras sobre a desviación do grosor da parede do tubo.Durante moito tempo, o problema do grosor desigual da parede e a desviación excesiva da parede do tubo do colector de escape azoutou moitas fundicións do colector de escape.

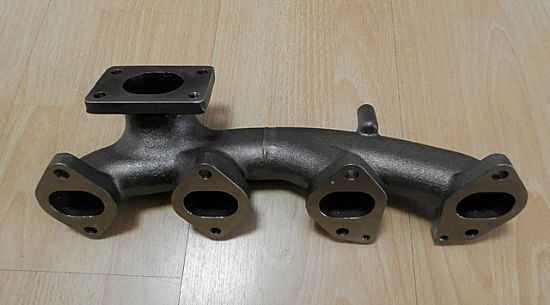
Unha fundición utilizou primeiro núcleos de area revestidos de area de sílice para producir colectores de escape de aceiro resistentes á calor.Debido á alta temperatura de vertedura (1470-1550 °C), os núcleos de area deformáronse facilmente, o que provocou fenómenos de fóra de tolerancia no grosor da parede da tubaxe.Aínda que a area de sílice foi tratada cun cambio de fase a alta temperatura, debido á influencia de varios factores, aínda non pode superar a deformación do núcleo de area a altas temperaturas, o que provoca unha gran variedade de flutuacións no espesor da parede do tubo. , e en casos graves, será descartado.Para mellorar a resistencia do núcleo de area e controlar a xeración de gas do núcleo de area, decidiuse utilizar area recuberta de area cerámica.Cando a cantidade de resina engadida foi un 36% menor que a da area recuberta de area de sílice, a súa resistencia á flexión a temperatura ambiente e á súa resistencia á flexión térmica aumentaron nun 51%, 67% e a cantidade de xeración de gas redúcese nun 20%, o que cumpre o estándar. requisitos de proceso de alta resistencia e baixa xeración de gas.
A fábrica utiliza núcleos de area revestidos de area de sílice e núcleos de area revestidos de area de cerámica para a fundición simultánea, despois de limpar as pezas de fundición, realizan inspeccións anatómicas.
Se o núcleo está feito de area revestida de area de sílice, as pezas de fundición teñen un grosor de parede irregular e unha parede fina, e o grosor da parede é de 3,0-6,2 mm;cando o núcleo está feito de area revestida de area cerámica, o grosor da parede da fundición é uniforme e o grosor da parede é de 4,4-4,6 mm.como a seguinte imaxe
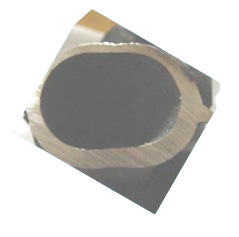
Area recuberta de area de sílice
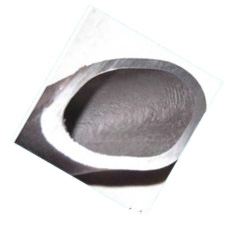
Arena recuberta de area cerámica
A area recuberta de area de cerámica úsase para facer núcleos, o que elimina a rotura do núcleo de area, reduce a deformación do núcleo de area, mellora moito a precisión dimensional da canle de fluxo da cavidade interna do colector de escape e reduce a adherencia da area na cavidade interna, mellorando a calidade do as fundicións e os produtos acabados cotizan e obtiveron importantes beneficios económicos.
3. Aplicación de area cerámica na carcasa do turbocompresor
A temperatura de traballo no extremo da turbina da carcasa do turbocompresor xeralmente supera os 600 °C, e algúns chegan ata os 950-1050 °C.O material da casca debe ser resistente ás altas temperaturas e ter un bo rendemento de fundición.A estrutura da cuncha é máis compacta, o grosor da parede é fino e uniforme, e a cavidade interior está limpa, etc., é moi esixente.Na actualidade, a carcasa do turbocompresor está feita xeralmente de aceiro fundido resistente á calor (como 1.4837 e 1.4849 da norma alemá DIN EN 10295), e tamén se utiliza ferro dúctil resistente á calor (como o estándar alemán GGG SiMo, o americano ferro nodular austenítico estándar de alto níquel D5S, etc.).
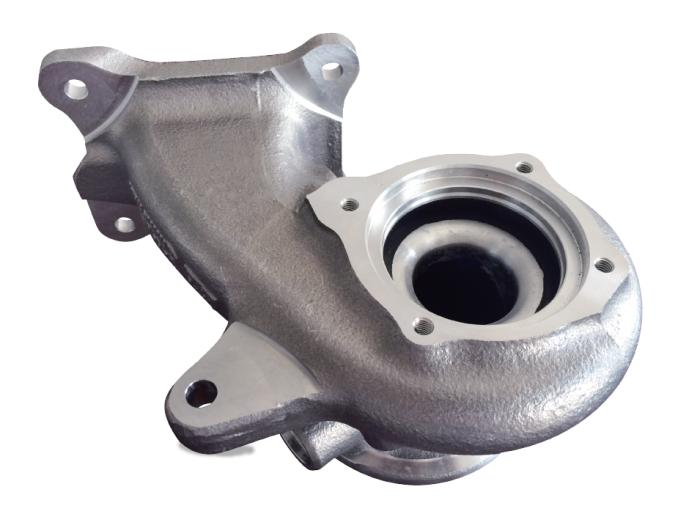
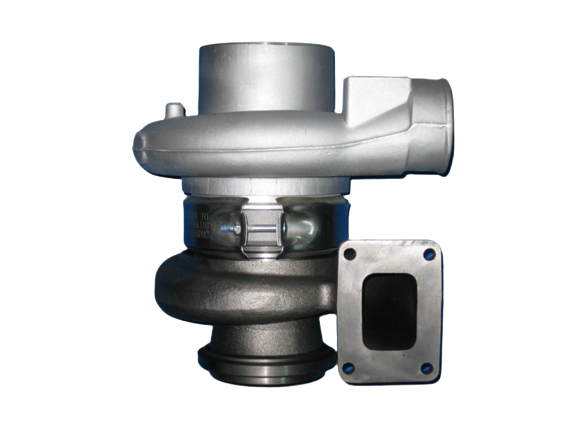
Carcasa do turbocompresor do motor 1,8 T, material: 1,4837, é dicir, GX40CrNiSi 25-12, composición química principal (%): C: 0,3-0,5, Si: 1-2,5, Cr: 24-27, Mo: Max 0,5, Ni: 11 -14, temperatura de vertedura 1560 ℃.A aliaxe ten un alto punto de fusión, unha gran taxa de encollemento, unha forte tendencia de rachadura en quente e unha alta dificultade de fundición.A estrutura metalográfica da fundición ten requisitos estritos sobre carburos residuais e inclusións non metálicas, e tamén hai regulacións específicas sobre defectos de fundición.Co fin de garantir a calidade e a eficiencia da produción das pezas de fundición, o proceso de moldaxe adopta a fundición do núcleo con núcleos de casca de area revestidos de película (e algúns núcleos de caixas frías e quentes).Inicialmente utilizouse area de fregado AFS50, e despois utilizouse area de sílice tostada, pero problemas como a pegada á area, as rebabas, as fendas térmicas e os poros na cavidade interna apareceron en diferentes graos.
En base á investigación e probas, a fábrica decidiu usar area cerámica.Inicialmente comprou area revestida acabada (area 100% cerámica), e despois comprou equipos de rexeneración e revestimento, e optimizou continuamente o proceso durante o proceso de produción, use area de cerámica e area de fregado para mesturar area bruta.Na actualidade, a area revestida aplícase aproximadamente segundo a seguinte táboa:
Proceso de area cerámica revestida de area para carcasa do turbocompresor | ||||
Tamaño da area | Taxa de area cerámica % | % de adición de resina | Resistencia á flexión MPa | Saída de gas ml/g |
AFS50 | 30-50 | 1,6-1,9 | 6,5-8 | ≤12 |
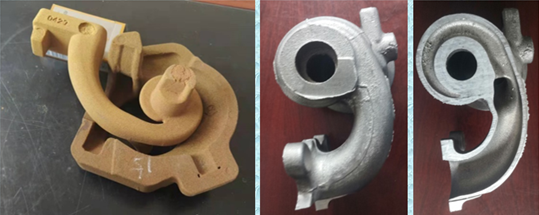
Durante os últimos anos, o proceso de produción desta planta estivo funcionando de forma estable, a calidade das pezas de fundición é boa e os beneficios económicos e ambientais son notables.O resumo é o seguinte:
a.Usar area cerámica, ou usar unha mestura de area de cerámica e area de sílice para facer núcleos, elimina defectos como a adherencia de area, a sinterización, as vetas e o craqueo térmico das pezas fundidas, e realiza unha produción estable e eficiente;
b.Fundición de núcleo, alta eficiencia de produción, baixa relación area-ferro (xeralmente non máis de 2:1), menor consumo de area bruta e custos máis baixos;
c.A vertedura do núcleo favorece a reciclaxe e a rexeneración global de residuos de area, e a recuperación térmica adóptase uniformemente para a rexeneración.O rendemento da area rexenerada alcanzou o nivel de area nova para fregar area, o que conseguiu o efecto de reducir o custo de compra de area bruta e reducir a descarga de residuos sólidos;
d.É necesario comprobar con frecuencia o contido de area cerámica en area rexenerada para determinar a cantidade de area cerámica nova engadida;
e.A area cerámica ten forma redonda, boa fluidez e gran especificidade.Cando se mestura con area de sílice, é fácil provocar a segregación.Se é necesario, o proceso de tiro de area debe ser axustado;
f.Ao cubrir a película, intente usar resina fenólica de alta calidade e use varios aditivos con precaución.
4. Aplicación de area cerámica na culata do motor de aliaxe de aluminio
Para mellorar a potencia dos automóbiles, reducir o consumo de combustible, reducir a contaminación dos gases de escape e protexer o medio ambiente, os automóbiles lixeiros son a tendencia de desenvolvemento da industria do automóbil.Na actualidade, as pezas de fundición de motores de automóbiles (incluído o motor diésel), como bloques de cilindros e culatas, adoitan ser fundidas con aliaxes de aluminio, e o proceso de fundición de bloques de cilindros e culatas, cando se usan núcleos de area, fundición por gravidade de moldes metálicos e baixa presión. casting (LPDC) son os máis representativos.
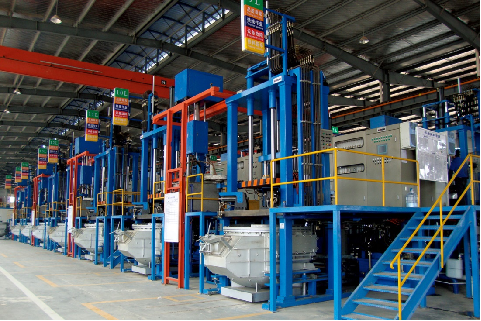
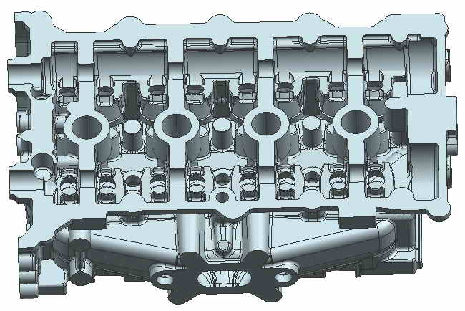
O núcleo de area, a area recuberta e o proceso de caixa fría do bloque de cilindros de aliaxe de aluminio e as fundicións da cabeza son máis comúns, adecuados para características de produción de alta precisión e gran escala.O método de uso de area cerámica é similar á produción de culata de ferro fundido.Debido á baixa temperatura de vertido e á pequena gravidade específica da aliaxe de aluminio, úsase xeralmente area de núcleo de baixa resistencia, como un núcleo de area de caixa fría nunha fábrica, a cantidade de resina engadida é do 0,5-0,6% e a resistencia á tracción é 0,8-1,2 MPa.Requírese area de núcleo Ten boa capacidade de plegabilidade.O uso de area cerámica reduce a cantidade de resina engadida e mellora moito o colapso do núcleo de area.
Nos últimos anos, co fin de mellorar o ambiente de produción e mellorar a calidade das fundicións, cada vez son máis as investigacións e aplicacións de aglutinantes inorgánicos (incluíndo vidro de auga modificado, aglutinantes de fosfato, etc.).A imaxe de abaixo é o lugar de fundición dunha fábrica que usa a culata de cilindro de aliaxe de aluminio de area cerámica con núcleo de aglutinante inorgánico.
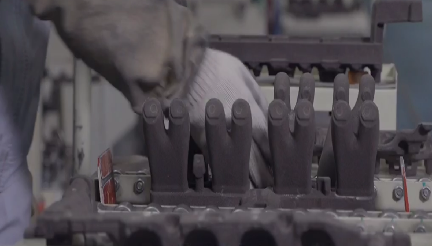
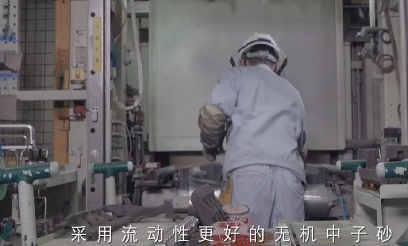
A fábrica usa un aglutinante inorgánico de area cerámica para facer o núcleo e a cantidade de aglutinante engadido é do 1,8 ao 2,2%.Debido á boa fluidez da area cerámica, o núcleo de area é denso, a superficie é completa e lisa e, ao mesmo tempo, a cantidade de xeración de gas é pequena, mellora moito o rendemento das pezas de fundición, mellora a colapsidade da area do núcleo. , mellora o ambiente de produción, e convértese nun modelo de produción verde.
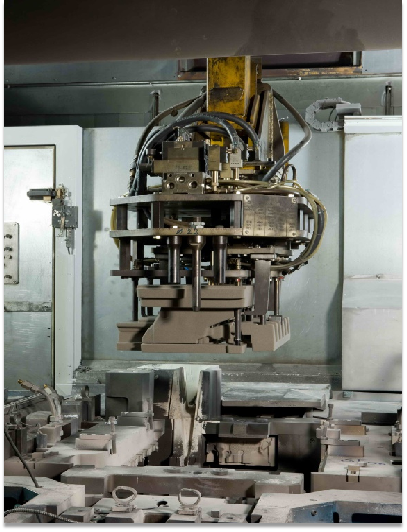
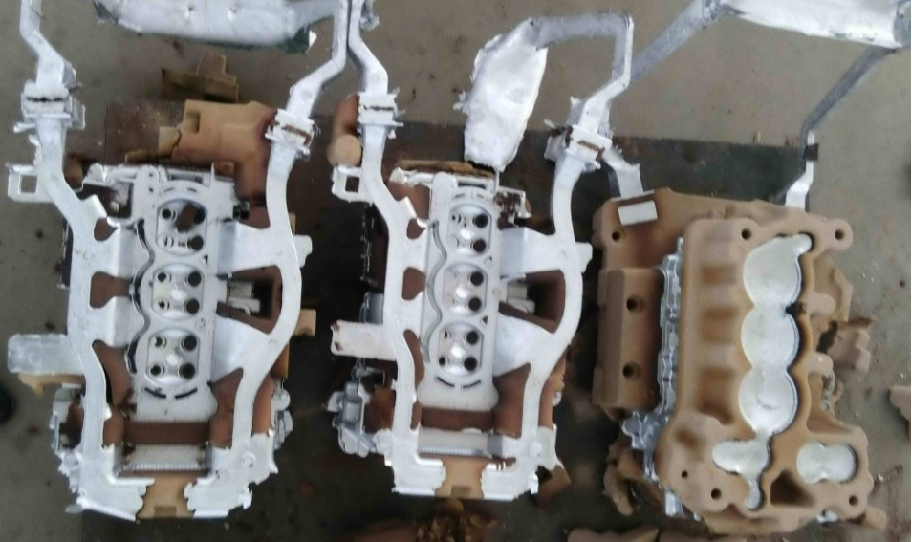
A aplicación de area cerámica na industria de fundición de motores mellorou a eficiencia da produción, mellorou o ambiente de traballo, resolveu defectos de fundición e conseguiu importantes beneficios económicos e bos beneficios ambientais.
A industria de fundición de motores debe seguir aumentando a rexeneración da area de núcleo, mellorar aínda máis a eficiencia de uso da area cerámica e reducir as emisións de residuos sólidos.
Desde a perspectiva do efecto de uso e do alcance de uso, a area cerámica é actualmente a area especial de fundición co mellor rendemento integral e o maior consumo na industria de fundición de motores.
Hora de publicación: 27-mar-2023